The impact of Electrification on Railway Connectivity
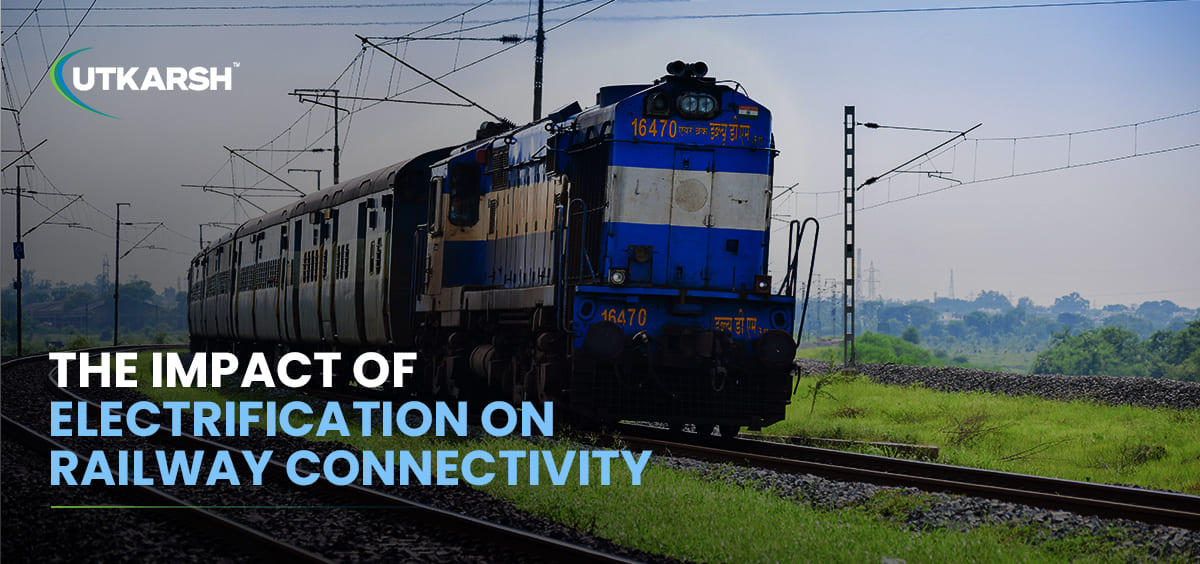
Railways have played a significant role in shaping India's transport system over the years. It has connected places and people from different regions of the country, making travel easier and faster. It has enhanced the country’s economy and provided jobs to many. When the government introduced the idea of railway electrification in the 1920s, there were several reasons that were behind it:
Electrification of railways would make travel faster and reduce the number of trips to the same destination.
Compared to diesel-powered trains, they would provide greater speed with lower maintenance requirements. This reduces the operational expenses of the trains, which in turn affects the ticket prices for passengers.
Electric trains do not vibrate like diesel trains and provide enhanced passenger comfort and safety.
Electric trains are also environmentally friendly.
In this article, we will explore how railway electrification in India enhances connectivity by improving reliability, speed and efficiency.
Improved speed: The electrification of railways has improved the speed of the trains considerably. This has enhanced the reliability of trains. Since electric trains have better speed in comparison with diesel run trains, similar distances have been covered in shorter spans.
Electric trains offer smooth transportation services and have enhanced passenger experience over the years. This has led to the introduction of new trains that are faster and offer better travel experience. Railway authorities can now focus better on passenger comfort and safety. For instance, the Rajdhani Express and Shatabdi Express run between different states and are the fastest trains in the country. They offer various services with heightened comfort during travels.
Improved reliability: One of the significant benefits of electrification is its ability to reduce the frequency of breakdowns caused by mechanical failures, thus enhancing the reliability of trains. Mechanical failures are a common issue that leads to train delays and cancellations, causing significant inconvenience to passengers. By eliminating these failures, electrification ensures that trains can operate more frequently and consistently, providing passengers with a more reliable service.
Improved efficiency: Electric trains are known for their superior energy efficiency when compared to diesel trains. This means that they consume less fuel, resulting in lower operational costs and a reduction in greenhouse gas emissions. Electrification also significantly improves the capacity of the railways to accommodate more passengers and freight. This is because electric trains are capable of running faster and smoother than their diesel counterparts, which translates into shorter travel times and increased service frequency.
Are you looking for Railway Electrification Structures?
Explore our range of Railway electrification structures. Let us discuss some of the features of our products:
RSJ & BFB mast- Supply range, A. Construction- OHE Structure, B. Attachment - As per site approved design, C. Body- Hot Dip Galvanised (610 GM/SQM or 1000 GM/SQM), Height - 9.5 m, 11.4 m & 12.4 m Standard Length. / Beyond those sections.(Custom). Our production capacity is 48,000 MT per Annum. Our products are specified as per CORE and RVNL standards. They are designed as per RDSO (Ref No. ETI OHE G 00144). The steel is sourced only from SAIL and/or CORE approved Re-Rollers manufacturing using SAIL material. They are CORE Part – I Approved for both the plants (i.e. Gurap & Jangalpur).
B-Series Mast- Supply Range, A. Construction - OHE structure, B. Attachment - As per site approved design, C. Body - Hot Dip Galvanised (610 GM/SQM or 1000 GM/SQM), Height - 9.5 m Standard Length. / Beyond 9.5 m Section.(Custom). Our production capacity is 30,000 MT per annum. These masts are made conforming to guidelines for OHE masts, TTC, PORTAL as per CORE STR NO- CORE-STR-01. They are designed as per RDSO (Ref No. ETI C 0071). Special High Grade Zinc (99.995% purity) procured from Hindustan Zinc Limited is used to produce B-Series Masts.
TTC Mast- Supply Range, A. Construction - OHE structure, B. Attachment - As per site approved design, C. Body - Hot Dip Galvanised (610 GM/SQM or 1000 GM/SQM), Height - 10.135 m Standard Length. and Boom 5.5 m & 8.0 m / Beyond those Section.(Custom). We follow guidelines for SPS & TSS as per CORE STR NO. - CORE-STR-01/A. TFT Masts are designed as per RDSO (Ref No: ETI C 0009 69 R B SH-3, ETI C 0009 69 R B SH-1, ETI C 0009 69 R C SH-2, ETI C 0009 69 R C SH-5, ETI C 0009 69 RC SH-4.
PORTALS - Supply Range, A. Construction - OHE structure, B. Attachment - As per site approved design, C. Body - Hot Dip Galvanised (610 GM/SQM or 1000 GM/SQM), Height - Based on type of the Portal i.e. O Type, N Type, R Type, G Type, S Type etc. our production capacity is 18000 MT per annum. The design specification are as follows: Portals- As per RDSO (Ref No: ETI C 0017 70 R B SH-4, ETI C 0017 70 RB SH-5, ETI C 0011 69 SH 5, ETI C 0011 69 SH 6, ET IC 0017 70 R B SH-2, ETI C 0008 R A SH-1, ETI C 0008 R B SH-2, ETI C 0008 R B SH-4, ETI C 0008 R C SH-3, ETI C 0008 R C SH-5, ETI C 0008 RA SH-6, ETI C 0011 69 R C SH-1, ETI C 0011 69 R C SH-2, ETI C 0011 69 R D SH-3, ETI C 0011 69 SH 4, ETI C 0017 70 R A SH-1, ETI C 0017 70 R A SH-6, ETI C 0017 70 R B SH-3. complete inspection (both stage and final) is carried out within 20-25 days through RITES.
SPS along with TSS & SSP- Supply Range, A. Construction - OHE structure, B. Attachment - As per site approved design, C. Body - Hot Dip Galvanised (610 GM/SQM or 1000 GM/SQM), Height - Fitting accessories for Mast, TTC & Portals. For Galvanizing (Process Control) - IS 2629, IS 2633 is followed. The design specifications are as per RDSO (Ref No. ETI C 0076 Rev. C, ETI OHE P 3231, ETI OHE P 3121, etc).