As India’s leading manufacturer & supplier of high-end engineering products, we offer high-quality PLB HDPE ducts made from virgin, UV-grade HDPE materials to ensure optimal performance for copper cable and optic fibre deployment. These products adhere to global and TEC standards, guaranteeing durability and reliability across various applications. The ducts consist of two concentric layers: the outer layer is HDPE, co-extruded with an inner layer of solid permanent lubricant (silicon) to reduce the internal coefficient of friction (ICF). This design increases resistance to mechanical and natural damage, thereby improving cable protection.
When considering PLB HDPEDucts options, one must also take into account the PLB HDPE Ducts price, which can vary based on the diameter, length, and additional features of the pipe. It's essential to compare the PLB HDPE Ducts price from different suppliers to ensure you get the best value for your investment.
We maintain a ready stock available at reasonable prices, ensuring fast delivery to meet urgent demands. The raw materials are sourced from major industry players, guaranteeing high quality. We have earned a stellar reputation in both government and private sectors for our reliable and efficient service. Our commitment to delivering exceptional quality has made us the top PLB HDPE Ducts manufacturer & supplier in India and abroad.
Utkarsh PLB HDPE Ducts are designed to minimise internal friction because of the innovative co-extrusion design that reduces the internal coefficient of friction (ICF). This feature helps lower the risk of friction-related damages and facilitates smooth cable installation, which makes our items ideal for telecom and infrastructure projects throughout Eastern India.
-
32/26, 40/33, 50/42
Sizes
-
50
Product Service Life
-
50
Years of Expertise
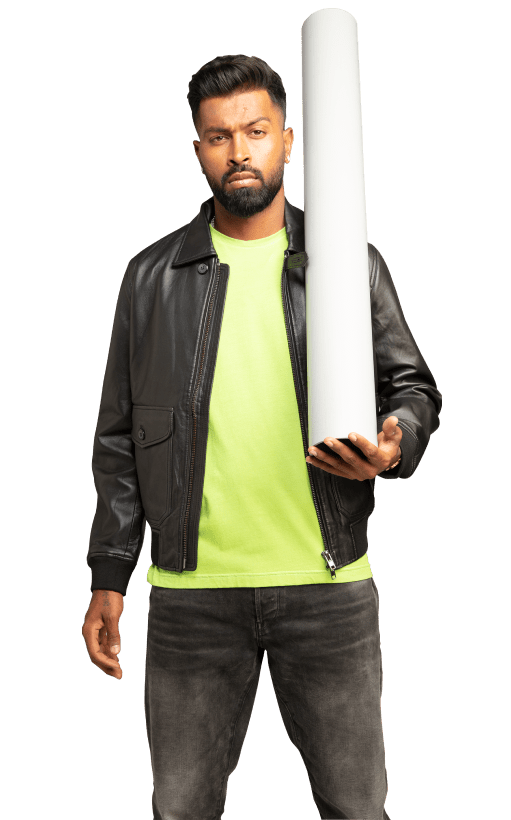
Manufacturing Process
A meticulous manufacturing process is followed for our range of PLB HDPE ducts, right from raw material selection through final inspection and packaging.
-
Raw Material Preparation
The raw materials and pigments are fed into a mixer via an automatic system, using a pre-set recipe. The preheated granules are then sent to the extruder hopper.
-
Material Feeding
Material is introduced into the extruder through a hopper and controlled by a gravimetric or volumetric system to ensure accurate feeding.
-
Melting and Mixing
Inside the extruder barrel, the material is heated to its melting point, around 200°C, through a combination of load (melt pressure) and friction in the screw system.
-
Pipe Formation
The melted material is pushed through a die-head (spider), where it is formed into a pipe shape.
-
Calibration and Cooling
The pipe is calibrated to the correct size in a vacuum sizing tank and then cooled with water in a spray tank.
-
Printing and Cutting
At the end of the production line, pipes are printed and cut into lengths or coiled based on their intended use.
-
Quality Control and Dispatch
Pipes undergo online inspection and testing by QC. Following post-activity checks and final inspection by QA, the pipes are dispatched as per the delivery order.